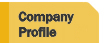 |
 |
Canadian Plastics, February 2005
New industrial blown film applications rely on more layers, reduced variability and higher throughput to provide customers with the right product for the right application at the right price
By John G. Smith
Discussions about plastic film inevitably turn to packaging applications, where contracts are measured in terms of massive volumes, but Davis-Standard marketing director Rick Keller is quick to point out why opportunities concerning industrial film shouldn't be overlooked.
"The general category is growing at probably as good a rate as food packaging [applications]," he says. "More and more, bigger things are being packaged in bags for protection."
It's good news for producers searching for new business still, industrial film presents its own share of challenges. Paul Waller, president of Plastics Touchpoint Group, Thornhill, ON, notes that producers have shifted to three-layer film in just a few years -even in what have been considered some of the last bastions of single-layer film - in a bid to limit the use of pricey resin to the outer skins of products, and to increase the outputs of individual production lines.
"It's becoming increasingly difficult to be competitive using single layer film," he says. "Even in developing countries, you see a lot of manufacturers starting to focus on the low-end co-extrusion market."
The process-related challenges don't end there. "There is a trend in equipment to deliver better gauge, higher outputs, and making use of more layers in the structures to enhance different properties in the film," agrees Adolfo Edgar, marketing manager at Macro Engineering (Mississauga, ON), which supplies extrusion and co-extrusion equipment, and winding systems.
Still, most producers continue to focus on "incremental improvements" in their existing lines, he says, noting how automatic gauge controls for blown film have only recently been "coming of age," even though they've been available for several years. New three-layer lines now tend to be fully computerized, while the controls were considered an option just a few years ago.
Some processors producing stretch wrap are doing an end run around the entire throughput issue, shifting to cast film lines, which virtually double the 500-foot-per-minute output of their blown film counterparts, Waller says. The end product may not be as able to stretch in all directions, but it can be noticeably stronger in the direction that it's pulled off a roll - a valuable attribute for the stretch film used to encase pallets of goods.
Technology pushing throughput
Brampton Engineering, meanwhile, recently unveiled its AquaFrost system, offering a higher throughput and lower capital cost when compared to cast equipment. The water-quenched downward film process uses a BE SCD -3 stackable pancake die and other conventional components, but turns the process upside down. "Because of the short residence time in the SCD, there is less scrap produced during product changeovers," says R.L. Bud Smith, president and CEO.
Automation is playing an ever more critical role for film producers. "I've seen more of a shift in the last year in North America to implement more automation, both in line-control features and equipment to take some of the guesswork out the operation," says Mark Anderson, sales manager of Plast-Control Inc., (Newburyport,MA), a maker of extrusion process management technology and control software. And that offers both tighter yield controls and the automatic control of extruder speeds, which is particularly important when working with co-extruders. Without the automation, he notes, operators stand little chance of controlling the formulas associated with short production runs.
"There's hardly any new lines sold without them." Still, less than 30% of North America's existing lines are running with yield controls, and it can be difficult to promote the upgrades, he says. When resin prices are high, customers say they can't afford to invest; when resin prices drop, they don't think they need the upgrade.
To compound matters, some film producers may be confused about the equipment they already have, thinking that gravimetric batch blenders and gravimetric yield control are the same thing. "There's a world of difference between the two," Anderson explains, noting that the latter will lead to savings on every resin. It keeps film within spec's for average thickness, while batch controls don't monitor what's coming from the die.
Gravimetric controls are responsible for the all-important "repeatability" of a product, adds Rafael Castillo, president of Dual Spiral Systems in Hamilton, ON, referring to the importance of the systems. "It's automating the production phases, so you have a tighter control of what's being made."
Dual Spiral Systems has recently released a new coating for film dies that reduces the appearance of melt fractures, and accommodates more pounds per hour. The coating is applied to the lip set of the die.
Field trials for the new K05 Melt Fracture Coating have been completed at various film extrusion plants processing LLDPE and HDPE resins. "Previously, these companies were using between 500-1200 ppm of polymer processing aid (PPA) to eliminate melt fracture they were experiencing on their high output lines," Castillo explains. The high amount of LLDPE in the film structure makes melt fractures particularly common in the manufacturing of stretch film. But the coated die lips eliminated melt fractures, even after the PPA was removed.
Cooling critical
"In the vast majority of cases, the limiting factor in output [of the films] is not how much you can melt and pump out of the extruders, but how much you can cool," says Waller. If temperatures rise too high, he notes, the bubble can't be controlled, the quality and width of the film suffers, wrinkling increases, and gauge begins to vary.
Meanwhile, those producing geomembranes - the 40-to-100-mil sheets that line garbage dumps and ditches - need to pay particular attention to cooling systems, such as internal bubble cooling, if they hope to surpass production rates of 12 to 20 feet per minute, Waller says. And there's obviously growing interest in the application. When the Layfield Group recently announced a $5-million expansion at its Richmond Poly Films Division, a portion of the new capacity, courtesy of a Battenfeld Gloucester advanced co-extrusion production line, was earmarked for a new flexible geomembrane liner, along with multi-polymer membranes for difficult chemical and heat-resistant applications.
A number of other industrial applications are just beginning to emerge. Waller refers to a new form of insulation that has a sheet of aluminum foil sandwiched between bubble cap film to create a barrier that can control heat loss through radiation as well as convection. It's also being considered as a potential replacement for galvanized steel air ducts.
Traditionally, thicker films related to such applications have also needed to be cut manually, but a new Davis-Standard agricultural film winder has been unveiled to handle the challenge. "It's a major safety issue for plants," Keller says, noting how operators can potentially get their arms trapped in winders while they attempt to make manual cuts. "[The films are] also folded and gusseted, so that you have four layers of this film at once that you have to cut."
"New materials are moving the industry to thinner films with better strength and better puncture resistance. Multilayer co-extrusion is the best way to produce these new structures," Brampton's Smith says. "New and refined gauging technology along with improved polymers allows producers of industrial films to deliver the same product performance with thinner films and inherent lower costs."
But the low melt strengths and less-than-robust bubble stability of the new materials often make them more demanding, he suggests.
It seems the challenges continue.
John G. Smith is the owner of a freelance writing company and can be reached at wordsmithmedia@rogers.com
Canadian Plastics, February 2005 |
|  |